Conversion of synthesis gas into e-fuels and waxes
Fischer-Tropsch synthesis
Fischer-Tropsch synthesis is a chemical process in which a mixture of carbon monoxide (CO) and hydrogen (H₂), commonly referred to as synthesis gas, is converted into various hydrocarbon compounds such as liquid fuels and waxes. This process was developed by Franz Fischer and Hans Tropsch at the beginning of the 20th century and is of great importance for the production of synthetic fuels, particularly with regard to the conversion of renewable energy into chemical molecules and the reduction of greenhouse gas emissions.
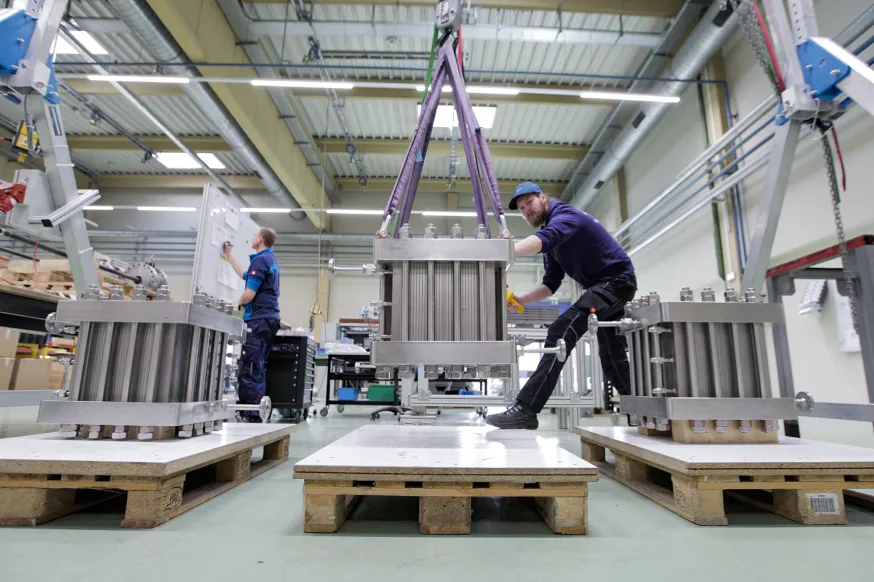
Production of synthesis gas (syngas)
Fischer-Tropsch synthesis begins with the production of syngas, a mixture of carbon monoxide and hydrogen. Syngas can be produced by various methods, including
Steam reforming: Steam reacts with natural gas or methane (CH4) to produce hydrogen and carbon monoxide. This is a common method for producing synthesis gas from fossil fuels.
Gasification: Biomass, coal or other carbonaceous materials are heated in a controlled environment with little oxygen, producing a mixture of carbon monoxide and hydrogen.
Partial oxidation: Synthesis gas is produced by controlled partial oxidation of hydrocarbons such as methane or coal.
Reverse water gas shift: The conversion of carbon dioxide into carbon monoxide with the aid of an excess of electrochemically generated hydrogen (water electrolysis).
Electrochemical reduction: Electrochemical conversion of CO2 into CO by splitting off oxygen in a process similar to water electrolysis and electrochemically generated hydrogen (water electrolysis).
Fischer-Tropsch synthesis reaction
The Fischer-Tropsch reaction is catalyzed by metal catalysts, such as iron (Fe) or cobalt (Co), under elevated temperature and pressure conditions. The reaction comprises the following steps:
Adsorption: Carbon monoxide and hydrogen molecules are adsorbed on the catalyst surface.
Surface reactions: The carbon monoxide molecules are hydrogenated by hydrogen and form hydrocarbon chains (compounds between carbon atoms) with the elimination of oxygen in the form of water. These hydrocarbons can range from linear and branched alkanes (hydrocarbons completely saturated with hydrogen) to compounds with double bonds between the carbon atoms or even compounds containing oxygen (alcohols and carboxylic acids).
The formation of bonds between carbon atoms is known as chain growth. Each bond between carbon atoms corresponds to a polymerization. If the bonds between carbon atoms branch in two directions, this process is called isomerization.
Desorption: The products water and hydrocarbon chains formed on the surface are initially still bound to the catalyst surface and are desorbed from the surface with a certain probability, which depends on pressure and temperature. This release of the hydrocarbons from the surface corresponds to a so-called chain termination. This chain termination is usually caused by the complete dehydrogenation of the terminal carbon atom, by incomplete hydrogenation of two neighboring carbon atoms to form a double bond or, in rare cases, by the incorporation of one or two oxygen atoms to form an alcohol or a carboxylic acid.
The product spectrum: The resulting hydrocarbons can be in the form of gases, liquids and solid waxes at room temperature, depending on the catalyst and reaction conditions.
Product applications
The products obtained from the Fischer-Tropsch synthesis have various uses, including:
Liquid fuels: The process can be used to produce synthetic liquid fuels that can be used as an alternative to conventional petroleum-based fuels. These fuels include synthetic diesel, turbine fuel (kerosene) and gasoline.
Waxes and lubricants: The process can also be used to obtain waxes that are used in candles, coatings and lubricants.
Chemical precursors: Some of the hydrocarbon products can serve as starting materials for the chemical industry and enable the production of various chemicals and polymers.
Fischer-Tropsch synthesis is a promising technology for the production of synthetic fuels with low to no carbon dioxide emissions. This depends heavily on the method used to produce the synthesis gas. If CO2 is extracted from biomass or from the air and hydrogen is produced using renewable energy, the CO2 cycle is closed and no additional greenhouse gas is produced through the combustion of the products. Economic and efficiency considerations continue to hamper their widespread use due to competition with cheap fossil fuels.