A significant mixture of gases
Synthesis gas
Synthesis gas is an important gas mixture that consists mainly of carbon monoxide (CO) and hydrogen (H2) and, as the name suggests, is used for syntheses. It is traditionally produced using various processes in which carbon-containing starting materials such as fossil fuels, biomass or waste materials are converted into a gas mixture. In connection with power-to-liquid or for the production of e-fuels, synthesis gas is produced from H2 and CO2 Synthesis gas is one of the most important gaseous intermediate products. It has a wide range of applications, from chemical synthesis to energy generation.
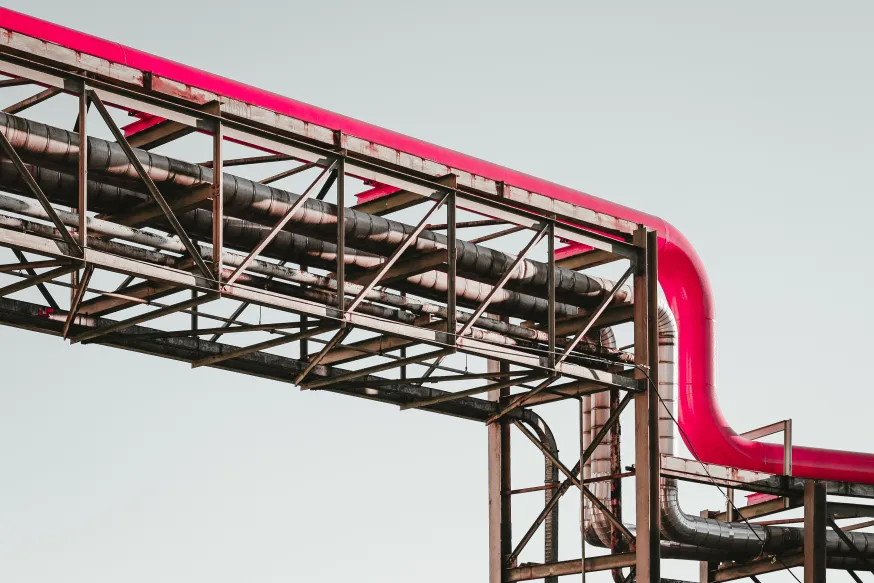
Composition and properties of synthesis gas
The composition of synthesis gas can vary depending on the source material and the specific production process, but generally consists of the following main components:
Carbon monoxide (CO): A colorless and odorless gas containing a carbon atom and an oxygen atom. CO is an important building block for many chemical processes.
Hydrogen (H2): A colorless, odorless gas consisting of two hydrogen atoms. Hydrogen is a clean energy carrier and is used in various industrial applications.
Carbon dioxide (CO2): A gas consisting of one carbon atom and two oxygen atoms. CO2 is a greenhouse gas and can be both a useful component and an undesirable impurity in synthesis gas.
Methane (CH4): A hydrocarbon gas consisting of one carbon atom and four hydrogen atoms. Methane can be contained in synthesis gas when feedstocks such as natural gas are used.
Nitrogen (N2): An inert gas that is often contained in synthesis gas due to its high occurrence in the atmosphere.
Trace impurities: Depending on the source material and production process, trace impurities such as sulphur compounds and particles may also be present in the synthesis gas.
Production of synthesis gas
Various processes are used in the production of synthesis gas, each of which is tailored to the raw material used:
Steam reforming: In this process, hydrocarbons such as propane, butane, ethane or methane (components of natural gas) react with water vapor (H2O) at high temperatures in the presence of a catalyst and produce synthesis gas. Hydrogen and carbon monoxide are released during the reaction, with CO2 being produced as a by-product. The disadvantage is the high heat requirement at high temperatures, which must be generated by burning a partial stream of the feedstock or other fuels.
Partial oxidation: In partial oxidation, a hydrocarbon feedstock is reacted with a limited (sub-stoichiometric) amount of oxygen or air. The reaction produces a mixture of CO and H2 as well as CO2 and water vapor. In contrast to steam reforming, this reaction is exothermic, meaning that heat energy is released and is therefore not optimal in terms of energy.
Autothermal reforming: Autothermal reforming is a combination of steam reforming and partial oxidation and is almost thermally neutral. The reactions can be combined in the same reaction chamber or in separate but thermally connected reaction chambers.
Biomass gasification: Biomass such as wood, agricultural residues and organic waste can be converted into synthesis gas through gasification. In this process, the biomass is heated in a controlled environment with limited oxygen and/or steam, resulting in the production of synthesis gas and solid residues (slag).
Coal gasification: Similar to biomass gasification, coal can also be converted into synthesis gas through gasification. Coal gasification is often used for industrial applications.
Reverse water gas shift (rWGS): For power-to-liquid processes or e-fuels, synthesis gas can be produced from hydrogen and carbon dioxide using the rWGS step. This produces the important molecule carbon monoxide and, as a by-product, water vapor. If an oversupply of hydrogen is added, all the important components for a synthesis gas are contained. The rWGS reaction requires an energy source, as the reaction is endothermic. The heat can be supplied electrically, e.g. in a chemical reactor or, partially electrochemically, in a solid oxide electrolysis cell (co-electrolysis).
Applications of synthesis gas
Synthesis gas is a versatile intermediate product with a wide range of applications:
Chemical synthesis: Synthesis gas serves as a building block for the production of various chemicals, including ammonia, methanol, synthetic fuels, plastics and more. It provides the necessary carbon and hydrogen atoms for the production of complex molecules.
Fuel production: Synthesis gas can be converted into synthetic fuels such as synthetic gasoline, diesel and aviation fuels using processes such as Fischer-Tropsch synthesis.
Power generation: Synthesis gas can be burned in gas turbines and combustion engines or used in combined cycle power plants to generate electricity.
Hydrogen production: Synthesis gas is a preliminary product for hydrogen production. The hydrogen content can be increased by processes such as the water-gas shift reaction (consumption of CO with water vapor in favor of hydrogen) or separated from the remaining components in the synthesis gas by membrane separation or pressure swing adsorption.
Environmental applications: Synthesis gas can be used for the remediation of waste materials or contaminated soils through processes such as thermal desorption or chemical reduction in situ.
Syngas plays a crucial role in the transition to a more sustainable and low-carbon energy system. It serves as a bridge between conventional fossil fuels and renewable energy sources, enabling the production of clean fuels, chemicals and hydrogen. In addition, syngas-based processes can facilitate the integration of renewable energy by converting excess energy into a storable form.
Synthesis gas is an important gas mixture consisting mainly of carbon monoxide and hydrogen. It is produced in various processes and serves as an important intermediate product in chemical synthesis, fuel production, electricity generation and environmental applications.